At the forefront of innovation, Caterpillar has been responsible for delivering the cuttingedge Next Gen range of equipment which has revolutionised the industry for the past couple of years.
These machines — typically 13 tonne to 95t excavators, medium wheel loaders, dozers from D4 up to D8, and motor graders from the 120 up to the 160 platform — incorporate advanced technology, superior efficiency, and sustainability features to address the evolving demands of global markets.
Earthmoving Equipment Magazine caught up with Greg Vaughan from Cat dealer Hastings Deering to discuss the features of
the new kids on the block, and how they’re so good that the models have established themselves as the definitive way of the future.
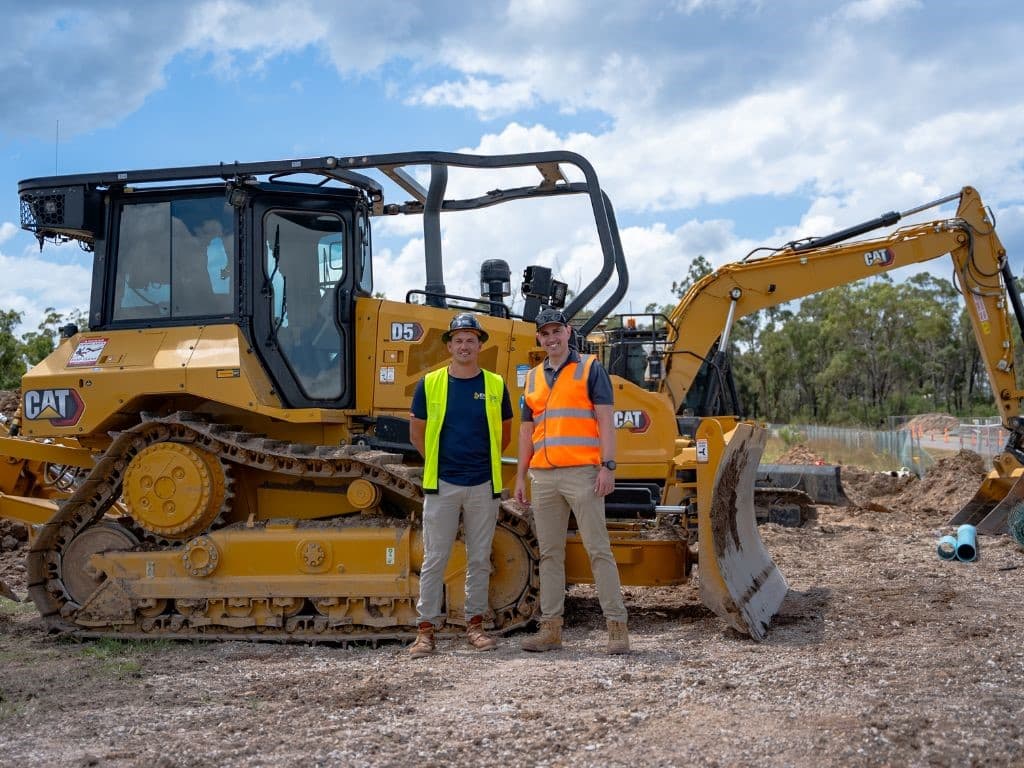
The Brisbane-based Business Manager for Hastings Deering’s Queensland division said the spark that lit the revolution was the company’s focus on three key areas that have helped the machines become clear leaders in their respective fields.
“The first priority was to drive down operational costs,” he said. “For example, we have extended service interval time, which of course drives down the ownership costs of the machines. “As a rule of thumb, nearly all our service intervals have now doubled across most of the Next Gen machines, decreasing running costs for businesses.”
The second point of importance was improving safety for operators. The plethora of initiatives that Caterpillar has come up with include factory options such as 360-degree cameras, improved lighting packages, ground level service checks, bigger window sizes through to reduced sizes of the posts for ROPS cabs. “The intent is to improve visibility as much as possible, one of the most key factors for an operator,” Greg said.
“Another safety factor is the improved operator environment, so reducing things such as operator movement and vibration coming through the seat reduces fatigue and therefore allows users to operate in a much safer environment.”
Greg said the comfortable seats were evident in all Next Gen models. “The vibrations are reduced and there are more adjustment settings to cater for operators of different heights and sizes,” he said. “They appreciate being able to get into a comfortable position to work, because if they are uncomfortable, that causes a lot of issues.
“The new settings also reduce operator movement, by placing everything from the radio, air con and all the other settings into the monitor, which is in front of the users, so they don’t have to lean around or reach out behind themselves to get into various positions to make different setting adjustments as needed.
“Everything's in front of the customers and at their hands, so that reduction in movement is a big reducer of fatigue for them as well.” Greg said Cat had spent great effort in making sure that the machines had much improved visibility. “Doubling the size of the back window in the excavators for example, so the operators have more visibility behind them,” he said. “Other improvements include moving back the front right toolbox about 60 centimetres, and slimming down the nose of the machines, giving better visibility to the right-hand corner. “There are also upgrade packages from Caterpillar which can detect people moving around the machines and gives operators better audio and a visual warning of objects that shouldn't be moving around the machines.”
Last, but not least, of the goals was the commitment to lift productivity, achieved through various technological and engineering innovations. As an example, Greg singled out the Cat Grade with 3D app, which helps grade complex designs using satellite positioning guidance for accuracy across large jobsites and multiple machines.
“Most opposition 3D systems have been manufactured and developed in isolation from the machine,” he said. “The Cat grade system was actually developed at the same time as the machine; it's in the machine’s DNA. “So all of the assist features that you find on the machine interlace themselves with the 3D system perfectly and seamlessly, so there's far less lagging as you use multiple features between the grade and assist features. The fact that they're all tied together just increases productivity.”
Cat Payload was another feature of the Next Gen machines that has been well-accepted by customers. The technology uses scales to ensure that trucks are loaded to optimum weight, with systems to track material and tonnage output. “It's probably one of the most used features we have across all of the assist features in the Next Gen platform,” Greg said.
“Firstly, it's just really easy to use. It's a great step up from previous generations. “Then it takes the guesswork out. When we're on the side of the road, with no weighbridges around us, the chain of responsibility comes back to the loader. “So without Payload, a contractor would have had to underload a truck out of safety to make sure that they didn't overload, so that if there was a safety incident, it wouldn't be held liable. “What the customer can do now is load that truck safely to capacity.
They know how much they've put in the machines. From a productivity standpoint and instead of leaving a tonne out of the truck, they can load their truck right up to capacity and send it safely on the way.” Greg said many of the features are now standard across the performance series machines and helped jobs get done faster. “People are more productive and they can get off the jobs and get paid quicker. One hour not worked means less fuel, less operated time and so on,” he said.
Greg was also excited about the dawn of 3D technology and its increasing use in construction and earthmoving applications. “One thing coming across multiple machine platforms right now that has excited us as a dealership, and I’m sure our customers, is the availability of 3D-ready machines,” he said. “Like all technology in the beginning, the hardware is the most expensive part due to the fact that there's a lot of research and development costs that go into that. “But I think we're over the hump now.
We have Next Gen dozers and excavators available from the factory with all of the 3D hardware on them, ready to be enabled if needed. “If you were a customer and you wanted to purchase a machine and you didn't have the need for 3D immediately, you could purchase a machine that had all of the hardware on at that reduced cost.
“Then if you have a job where you need 3D capability, you can simply call us and we'd be able to enable the machine for you on the spot. “That's a huge step forward for customers because they'll be able to buy machines that they're future proofing for 3D jobs. It’s available on the dozers and excavator now, and is coming out to the motor graders. “It allows customers to buy a machine that's ready to perform as 3D jobs become more prevalent across the industry.”
Greg said one of the strongest aspects of the Next Gen platform was commonality. “We've standardised most of our platforms across all of the Next Gen products, especially from an operator perspective, whether it be dozers, excavators or motor graders,” he said. “Very often, operators have to work on lots of different machinery types, and when they're jumping from one machine to the next, the controls are different, from the menu down to the seat adjustments, and it can be frustrating.
“With Next Gen machines, we're seeing a commonality across the board, things like even the colour of the adjustable levers on your seat as well as the same sort of monitors and user interface. “When you look inside a D5 dozer, the monitors are actually the same screens as you get in the Next Gen excavators, but just turned on their side.
“We're even seeing people able to move between different size class machines, say from a 13t excavator to a 95t excavator. Everything's all in the same place and identical. Then when they jump onto a dozer or a motor grader, they're able to move through the options and the settings of the machines so much easier because the Cat platform is standardized. “This is really the unsung hero of the Next Gen machines.”
IDC Construct
One of the Bundaberg businesses keenly supportive of the Next Gen evolution is IDC Construct, a dynamic building and construction company specialising in industrial, commercial and domestic development projects. Established under the leadership of Managing Director Kailen Berthelsen, IDC prides itself on innovation, efficiency, and high-quality delivery and 'building beyond the blueprints'.
“We do commercial and industrial projects. We do civil work all the way through to the construction and fit out,” he said. “Part of our point of difference is that we in fact do the civil operation as well as the construction work. That sets us apart from our competitors.”
As part of its operations, Kailen aims to provide employees with best-in-class equipment to ensure that the business operates efficiently on projects and ultimately deliver them to clients. And that means using the latest Cat equipment.
We spoke to Kailen at one of IDC’s projects, where a Cat Next Gen 315 excavator was digging up ground for a sewer extension, while a Cat D5 dozer was employed in concrete pavement preparation.
“For us, introducing Cat Grade with 3D to our fleet has been of tremendous benefit,” he said. “It ruled out a lot of error. We knew we could trust the operator to know what he had to do at what depth. “A large part of our work is concrete hard stand and it’s really important to be efficient in your subgrade preparation, to ensure the strength of the concrete and how much you're going to use.
“You don't want to have 30mm too much here, or 50mm too much there. It needs to be precise and the Cat Grade system gives us that, ensuring a lot of savings in our construction.” Kailen said the Cat Grade feature ensured that projects could be set up before operators even touched the ground.
“We'll have a design file and implement it into our base station across all the equipment,” he said. “Every part that functions in our construction can be governed before we even commence. “The GPS aspect of the machines is second to none.
“We recently completed a project the operator was able to set up an infield design using the Cat Grade’s GPS system and the project took around 40 per cent of the time that we'd actually allowed for.
“Since we implemented the Cat Grade system, our rechecks for construction show that the machines have been accurate. We've had to do no re-work; the outcome has been exactly what we needed.”
Other welcome features were Payload and the visibility and safety tools. “The ease-of-use function of Payload is really helpful when we're on the project, as we want to make sure that we don't overload trucks,” he said. “We always assess the size of the truck and what its carrying capacity is. This allows us to use the full potential to truck without overloading.
“We can calculate the payload, ensure that the machine is doing what it can and we're keeping the trucks within their safety limit.” And all this while working in safety alongside roads, with operators knowing they are protected from passing traffic by an e-fence: Cat’s feature that automatically stops machine motion within a predefined work area you set to avoid hazards. “Safety is key when operating in the confined spaces that we find ourselves in,” Kailen said.
“The operator safety features of the equipment are second to none. “As well as the e-fence, our operators have the benefit of a 360° camera. They can view the sides, front, rear, all of which adds to the safety of the operator and all those around him. “When operators are in a machine, they're focused on the task at hand.
The cameras around them enable clear visibility in all the spots that matter, and also make sure they're watching their backs and sides, making sure that no one else is at risk.”
Kailen said comfort was also a key factor. “Lots of space, visibility, great air conditioning, comfy seat, big open cabin. There's not much really more to ask for to make our staff comfortable,” he said. “For that reason, we find that our staff turnover is very low. People want to stay. They want to stay in the machine. “They enjoy their job. It is their space. But they spend a lot of time during the day in it. It is important for us that we have equipment that will really facilitate that.” In short, Kailen said his operators “really can't complain about much”.
“They're quite spoiled by these machines,” he said. “They are excellent machines which make the operator look really good! Even the best operator finds it very difficult to compete with the Cat Grade GPS for the various tasks.
“It’s an option up their sleeves that when they need to do some final trim work, for example, and they're getting tired, they can still produce the great outcome that we require. “As long as they're comfortable and safe in the machine, they can produce great outcomes.”
The Hastings Deering connection
When it comes to sourcing the equipment, IDC goes straight to Hastings Deering, and Greg. “They’re a clear choice for me. I've had their equipment over the years and the service, the support, the people, they're all really great,” Kailen said.
“It would be great to say that we don't ever have issues, but sometimes we have a breakdown or something's gone wrong. Fixing it is just a phone call away to Hastings Deering. “Downtime is important in our industry. Maybe we need to get in front of the weather or we've got a timeline where the work needs to be done. “We need to be able to rely on a company that can service us after the sale. And Hastings Deering does that better than anyone else.
“One of the attributes we aim for is to be fastpaced and flexible. It's important to us. “And Hastings Deering and Caterpillar are aligned with these values of ours. Things need to be done. We need to do it fast, but we do need to stay flexible. You can't be rigid.
“We can't wait three months for a machine. If there's stock at Hastings Deering and it's available, they'll do everything they can to get it to us when we need it.
“Each job will call for certain things, and sometimes we need to make the investment then and there. And Hastings Deering is absolutely flexible in that regard.”
Greg said Hastings Deering was one of the top five Cat dealers in the world, and therefore had a lot of equipment available for customers to purchase on the ground. “We have really strong stockholdings and we know that that's a real key part of our success that we can supply machines quickly,” he said. “We know jobs are dynamic and projects are awarded very sporadically and sometimes, companies are required to get going very quickly and they don't have the opportunity to wait six months for a machine to come in.
“Our presence is huge. We are one of the biggest Cat dealerships in Australia and we have the most technicians in the regions. “As we always say, the rep may sell the first machine, but our servicing back-up sells the second.”
Greg said customers had access to a call centre 24/7. “We always have standby people on those lines to make sure if a customer has a problem with the machine, they have a port of call,” he said. “Whether late at night or on the weekend, we have the ability to support our customers in so many different ways."
The final word comes from Kailen, who said Cat machines and Caterpillar in general had long been class leaders, always looking at the cutting edge of technology. “As a building company, we associate ourselves in the same way.
We always want to look for the next best thing that people are creating to make life easier for us and get better outcomes,” he said.
“One of our sayings is that our construction is ground-breaking before we break ground. And that means implementing the latest technology. “We want to continue to evolve in the way we do things and always look to a better way and we feel that Caterpillar is exactly the same in that regard.”